increase in speed of deployment
GKN Powder Metallurgy had already started to install vision systems to handle visual inspection in some of their production facilities. The company wanted to increase deployment speed of these systems and study how accuracy rates can be increased. Furthermore it was important to become less dependent (a) on highly qualified and hard to find engineering personnel that would program the software of vision systems and (b) on qualified end visual inspection personell. GKN Powder Metallurgy achieved that by deploying our computer vision and machine learning based software solution to existing vision systems and is considering to work with us on installment of our vision system (hardware and software) on new production lines.
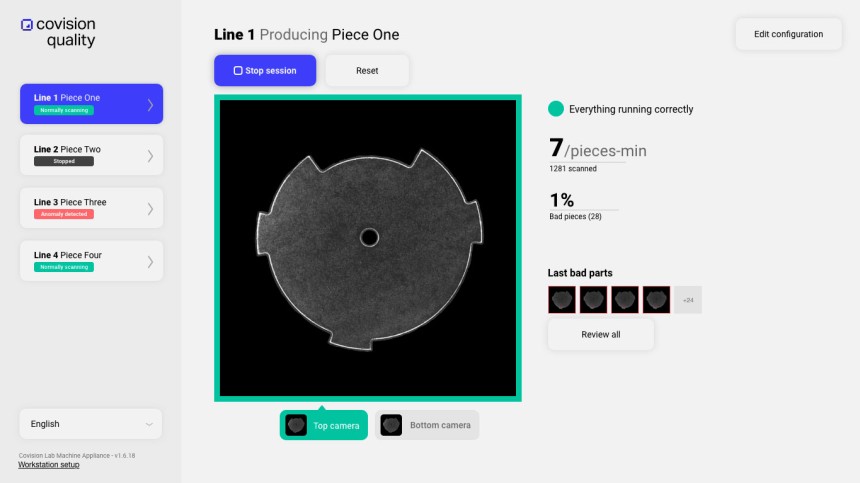