GKN uses our technology to get more accurate classification of defects and to scale visual inspection quickly from one part to another and from one production line to many.
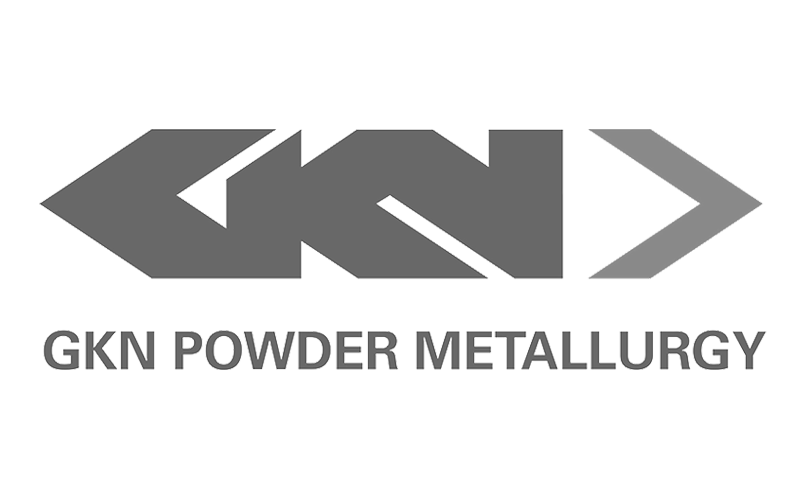
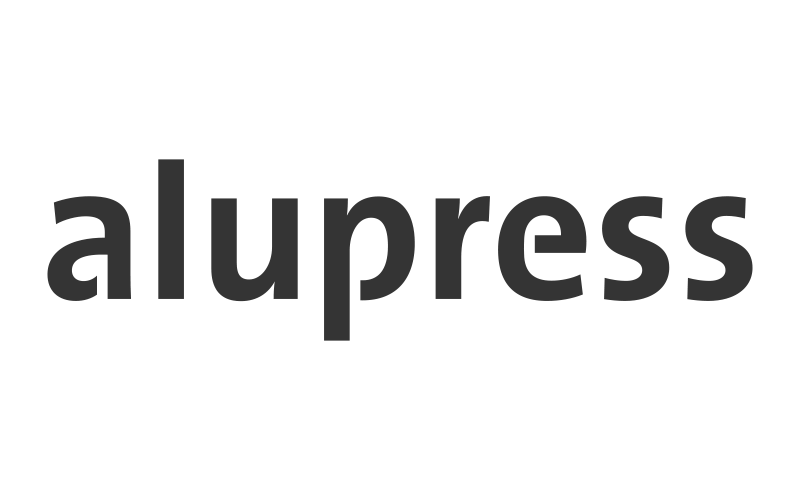
Alupress uses our technology to speed-up cycle times on complex parts by leveraging our 3D based machine learning approach. Furthermore, Alupress increases classification accuracy and saves costs.
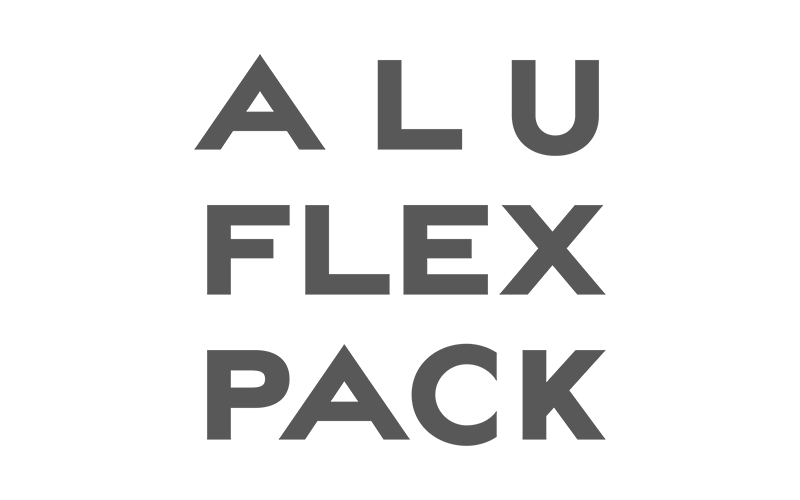
Aluflexpack - a leading international manufacturer of flexible packaging - is leveraging our machine learning based visual inspection software to automate end-of-line quality control. The collaboration started in the plants in Croatia.
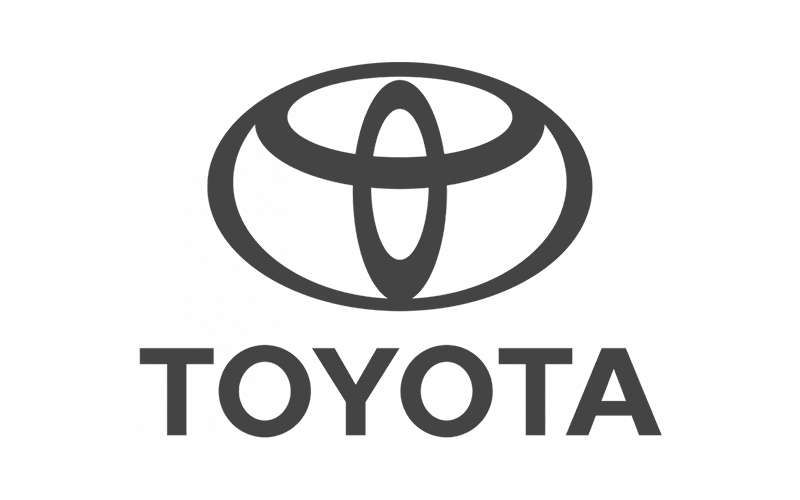
Toyota is one of the largest global car manufacturers. We are working with Toyota Motor Europe to leverage our unsupervised machine learning software to automate visual inspection on metal parts.
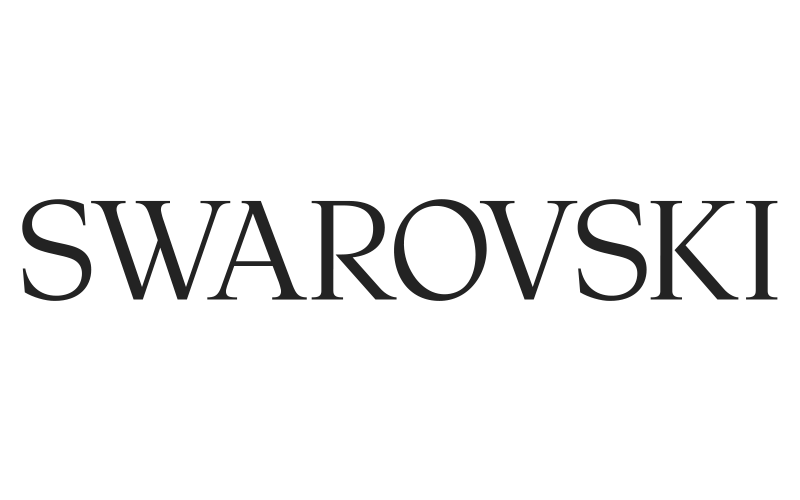
Swarovski is a globally recognized producer of crystal glass and jewelry. We work with the company to leverage our unsupervised machine learning approach to have Swarovski employees train new models quickly and hence scale reliably to many production lines.
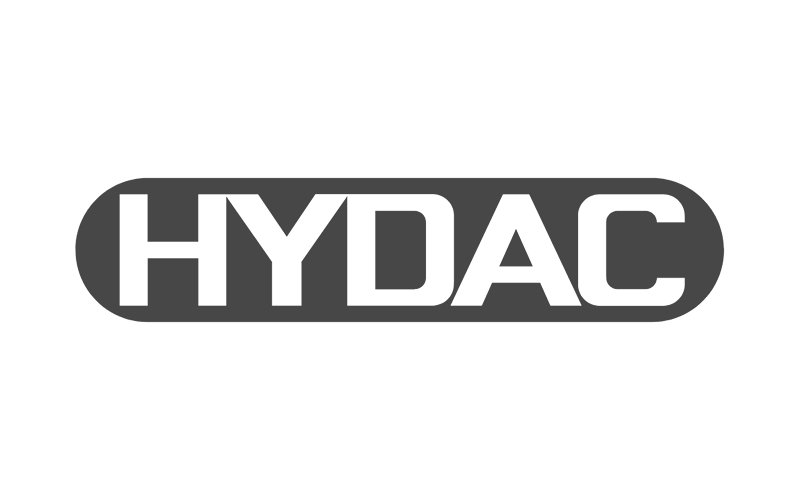
Hydac is an international company group that specializes in production and distribution of components and systems related to hydraulics and fluidics. We work with Hydac on analyzing the usage of supervised and unsupervised ML approaches.